Елена Бондаренко - Техническая эксплуатация и ремонт технологического оборудования Страница 2
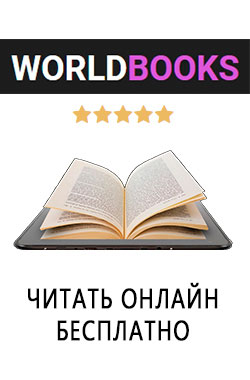
- Категория: Научные и научно-популярные книги / Техническая литература
- Автор: Елена Бондаренко
- Год выпуска: неизвестен
- ISBN: нет данных
- Издательство: -
- Страниц: 11
- Добавлено: 2019-02-02 16:59:31
Елена Бондаренко - Техническая эксплуатация и ремонт технологического оборудования краткое содержание
Прочтите описание перед тем, как прочитать онлайн книгу «Елена Бондаренко - Техническая эксплуатация и ремонт технологического оборудования» бесплатно полную версию:В пособии рассмотрены организационные принципы производственной эксплуатации общепромышленного оборудования. Даны особенности построения системы технической эксплуатации и ремонта оборудования предприятий автомобильного транспорта.
Елена Бондаренко - Техническая эксплуатация и ремонт технологического оборудования читать онлайн бесплатно
Порядок выполнения работ по ТО, текущему и капитальному ремонтам разрабатывается заводами – изготовителями оборудования. Этот порядок определяется в инструкциях по эксплуатации соответствующих машин и неукоснительно выполняется на производственных предприятиях.
Еще одна существенная особенность ремонтного производства заключается в том, что ремонт с полной разборкой оборудования практически не применяется. Как текущий, так и капитальный ремонты выполняются путем замены пришедших в негодность агрегатов, узлов и деталей на годные заводского изготовления. Ремонтно-механические цеха по изготовлению и восстановлению деталей отсутствуют.
В США существует система планово-предупредительного обслуживания основных фондов, которая предусматривает содержание основных фондов в работоспособном состоянии путем замены любого сменного элемента, если есть опасность выхода оборудования из строя. Для обеспечения возможности восстановления оборудования путем замены отдельных агрегатов, узлов и деталей предприятия-изготовители резервируют до 25 % своих производственных мощностей для выпуска такой продукции. Доля выполнения ремонтных работ силами специализированных ремонтных фирм не превышает 10 % всего объема ремонтов в стране. Преимущественно это наладка, испытания, модернизация, сложные регулировочные работы, реже – замена сложных агрегатов.
Специалисты Японии и Южной Кореи считают, что для значительного увеличения прибыли от эксплуатации оборудования необходимо, чтобы ремонтновосстановительное производство носило ритмичный (плановый) характер, как и в основном производстве. В японской системе обеспечения сохранности оборудования заложен следующий принцип: все работы по замене агрегатов, узлов и деталей самой сложной машины по возможности следует производить на месте ее установки силами собственного специально подготовленного персонала.
Во всех зарубежных странах большое внимание уделяется нормированию затрат труда, времени остановки на восстановление работоспособности машин и времени плановой замены сменных элементов. Снижение издержек на восстановление неисправных основных фондов – это необходимое условие эффективной работы на конкурентном рынке.
3 Реализация концепции системы ППР в отечественной практике. Отдел главного механика
Система ППР оборудования, сложившаяся в соответствии с требованиями ГОСТ 18322-78, представлена на рисунке 1. Она отличается от ремонтных технологий, принятых в зарубежных странах, направленностью на поддержание работоспособности оборудования путем проведения текущих и капитальных ремонтов.
Организация ТО и ремонта оборудования на основе системы ППР осуществляется отделом главного механика (ОГМ). Основная задача этого отдела – поддержание оборудования предприятия в постоянно работоспособном состоянии на основе ППР. Главный механик, возглавляющий отдел, несет полную ответственность перед руководством предприятия за технически исправное и работоспособное состояние всего оборудования предприятия. Ему подчинены ремонтно-механический и ремонтно-строительные цеха, а на небольших предприятиях – и энергетическое хозяйство.
Рисунок 1 – Дифференциация работ по системе планово – предупредительного ремонта.
В своей работе ОГМ руководствуется действующим законодательством, постановлениями Правительства РФ, приказами руководителя предприятия, действующими правилами безопасности, стандартами и инструкциями по эксплуатации оборудования заводов-изготовителей.
В задачи ОГМ входит также контроль соблюдения установленных норм простоя в ремонте и непрерывной работы оборудования между ремонтами, качества ремонта и состояния промышленной безопасности при производстве ремонта, выполнения эксплуатационными и ремонтными подразделениями функций по организации и осуществлению технического надзора за эксплуатацией оборудования.
ОГМ разрабатывает мероприятия по улучшению организации ремонта и эксплуатации оборудования, внедрению прогрессивных методов ремонта, сокращению трудоемкости ремонта, норм простоя оборудования в ремонте, экономии материалов и средств на проведение ТО и ремонта основных фондов предприятия.
Отдел участвует в работе по планированию технического развития производства, капитального ремонта и модернизации основных фондов, баланса производственных мощностей и их использования. Разрабатывает нормативные материалы по ТО и ремонту оборудования (нормы расхода материалов, деталей, агрегатов и узлов основного оборудования), привлекая в необходимых случаях сторонние организации, участвует в расследовании причин инцидентов и аварий оборудования, производственного травматизма, принимает меры по их предупреждению.
ОГМ осуществляет контроль соблюдения установленных сроков составления подразделениями ведомостей дефектов и смет затрат на ремонт оборудования, заявок на запасные части, материалы, инструмент; контролирует правильность их расходования. Готовит материалы для заключения договоров с предприятиямиизготовителями на поставку запасных частей и оборудования и со специализированными подрядными ремонтными организациями – на капитальный ремонт и модернизацию оборудования; осуществляет контроль расходования средств на эти цели.
ОГМ принимает участие в разработке и внедрении технических условий на капитальный ремонт оборудования. Дает заключения по рационализаторским предложениям и изобретениям, связанным с совершенствованием технологии и организации ремонтных работ, оказывает рационализаторам и изобретателям практическую помощь и организует внедрение принятых предложений.
ОГМ разрабатывает, согласовывает с подразделениями и службами предприятия и утверждает у руководителя предприятия форму организации ТО и ремонта оборудования.
4 Производственная эксплуатация оборудования
Под производственной эксплуатацией понимают стадию жизненного цикла оборудования, заключающуюся в его использовании по назначению. В стадию жизненного цикла оборудования входят следующие этапы: прием; монтаж; ввод в эксплуатацию; организация эксплуатации; служба в течение определенного срока; амортизация; хранение; выбытие оборудования.
4.1 Прием оборудования
Прием оборудования, поступившего от заводов-изготовителей на предприятие, производится комиссиями. Для основного оборудования председателем комиссии является главный инженер- заместитель руководителя предприятия, членами – главный механик, главный бухгалтер (бухгалтер) и руководитель подразделения по принадлежности оборудования, а также представители Ростехнадзора – для приема оборудования опасных производств. Остальное (неосновное) оборудование принимается комиссией, члены которой хорошо знакомы с устройством и эксплуатацией принимаемого оборудования.
Комиссии несут ответственность за строгое и точное соблюдение правил приемки оборудования, в том числе:
– внешний осмотр упаковки;
– состояния консервации открытых рабочих поверхностей;
– внешней отделки и защиты от повреждений отдельных выступающих частей и деталей оборудования;
– проверку фактической комплектности оборудования, запчастей, инструментов и технической документации с приложенными к прибывшему оборудованию спецификациями и упаковочными листами – наличия технической документации, которую заводы-изготовители обязаны присылать вместе с поставляемым оборудованием согласно разделу «Комплектация» технических условий на поставку и в соответствии с ГОСТ 2.601-2006;
– обнаружение явных дефектов в оборудовании, видимых без его разборки.
При приемке оборудования должна быть обеспечена правильная его разгрузка с железнодорожных платформ и вагонов, грузовых автомобилей или иных видов транспортных средств. Транспортировка оборудования, упакованного в специальную тару, должна производиться в соответствии с предупредительными и манипуляционными знаками. (Приложение А) Персонал, осуществляющий разгрузку прибывшего оборудования, должен быть подготовлен к работе по сохранению оборудования в целости и предотвращения поломок или повреждений, которые могут отрицательно повлиять на работу оборудования в период эксплуатации.
Акты приема-передачи оборудования, полностью оформленные и подписанные всеми членами комиссии, передаются в бухгалтерию предприятия для балансового учета, где оборудованию присваивается инвентарный номер. При определении состава каждого инвентарного объекта следует руководствоваться Общероссийским классификатором основных фондов (ОКОФ), утвержденным постановлением Государственного комитета РФ по стандартизации, метрологии и сертификации от 26 декабря 1994 г. № 359.
Жалоба
Напишите нам, и мы в срочном порядке примем меры.